Contact Jin Zhanrui
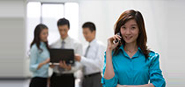
24-hour hotline: 138-2693-8913
Phone: 0769-82663318
E-mail: kingruizhao@kingruimold.com
Address: Room 201, Building 1, No. 376 Zhen'an Middle Road, Chang'an Town, Dongguan City, Guangdong Province
Home >News > common problem >
What is mold?
Article source:
Published time:2016-03-30 15:38:55
Press Die processing metal processing classification, commonly used are: stamping die, including stamping die, bending die, drawing die, flanging die, necking die, mold and downs, bulging mold, plastic molds; forging dies, including forging with forging die, upsetting die and the like; and the extrusion die and die casting mold. Used in the manufacture of non-metallic and powder metallurgy mold press processing object naming and classification, plastic, rubber mold and powder metallurgy molds. 1. stamping die for sheet metal stamping and mold separation. Molding mold has a cavity, the mold separation bladed. The most commonly used stamping die only one station, a complete production process. This mold universal application, simple structure, easy to manufacture, but low productivity. To improve productivity, can be multi-channel stamping process, such as blanking, deep drawing, punching, trimming and other arrangements in the same mold, the blank to complete the multi-channel stamping process at the same work station, such a mold called a composite mold . Another would blanking, bending, deep drawing, punching and trimming and other work arrangements in different stations on the same mold, this mold called progressive die (also known as continuous mode). 2. die forging metal mold for hot forming. When forging blank tend to be made after repeated deformation forging, which requires a module on the engraved with several cavities. Each metal in turn sent to the cavity, and plastic flow in the cavity, the cavity is filled into the final forging. In forging forming, forging the blank is difficult and the final volume of the cavity is equal to, in order to avoid waste, stock selection is slightly larger. To this end, in the final forging die, the die cavity four weeks of the interface features flash tank to store excess metal forming will flash cut. Cavity should minimize sharp corners, deep grooves to facilitate metal plastic flow and filling, reduce mold wear and cracking, improve die life. 3. The extrusion die for extrusion molding metal mold. Positive extrusion die having a stationary die and the extrusion cylinder and disposed blank blank punch for exerting pressure. Extrusion of hollow parts, punch front end with a mandrel. Anti-extrusion die for the extrusion barrel die, become punch punch. Metal extrusion from the need to die under great pressure, the pressure required in the cold state up to 2000 kN / mm (200 kg / mm) or more. To this end, the anti-extrusion cylinder and the extrusion die need to have high strength, often using multi-layer prestressed composite structure. Punch and punch working length should be short to avoid instability and bending under high compressive stress. 4. The casting mold is mounted on a die-casting machine, the liquid metal into the cavity under high pressure, holding pressure to the metal solidification and shaping molds. It is mainly used for aluminum, zinc, copper, steel can also be used. Structure and plastic injection mold die casting mold similar. It consists of the movable mold and the fixed mold cavity constituted, formed by the bore of the casting core. Metal cavity is cooled, solidified out of the core, separated from the mold by ejector Release castings. General thin wall hollow casting, there are many sets of ribs, the shape of the complex structure, size requirements more precisely, surface is smooth, the molten metal at a high temperature molding. Therefore, die-casting mold manufacturing materials need to use high temperature. 5. The solid metal powder metallurgy molding press-mold forming. The metal powder quantitatively poured into the lower mold and the lower mold, closed molding, and then the ejector means ejecting the preforms. The preform into the sintering furnace sintering, then made of powder metallurgy parts. General powder metallurgy gap is large, about 15% of the total volume, the pressure is not formed, the mold structure is relatively simple, precision, surface roughness in general, so no special requirements for mold. In order to reduce the gap, increase the density and strength of the sintered blank, and then conduct a hot forging, known as powder forging. Used similar mold and die forging.
Precision machining, precision wire cutting, coordinate jig grinders